Application Modernization
Community Products
System architecture built to grow with the organization
How Orases helped plan and build a system to scale with future goals in mind.
Community Playthings manufactures quality maple furniture, toys, and equipment for early childhood settings. Rifton Equipment is a leading producer of adaptive equipment for people with disabilities, manufacturing equipment for special needs children and adults. All equipment is manufactured and configured to order.
Each factory (shop) has a shop foreman and an assistant foreman who is responsible to see that the daily work gets completed. Each factory also has at least one Design Engineer, Process Engineer, and QA. These engineers complete the work in the PMAN system which regulates the MES system and describes how the goods are manufactured.
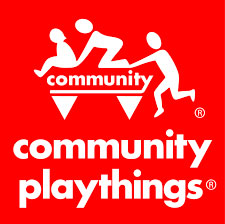
Client
Community Products
Project Name
POC and Pilot MEM 1.0
Services
- Application Modernization Services
- Custom Software Development Services
- Network Security
- Cybersecurity Advisory & Consulting
- Application Security Services
- Integration Consulting
- System Integration Services
- DevOps & DevSecOps
- Software Testing & QA Services
- UI/UX Design & Development Services
- Maintenance & Support
- Project Management Services For Software Development
The Challenge
Aging architecture weighed down with technical debt.
CP purchased Powercerv software in the 1990’s. Six months after they implemented it, Powercerv corporation went bankrupt. CP retained the Powerbuilder and SQL source code. In the early 2000’s CP rewrote the distribution and warehousing systems into a custom VB6 and SQL application and have continued to develop and extend the Manufacturing system in Powerbuilder building off the Powercerv Manufacturing (Pman) base.
The MES system was built as an extension to the Pman system using the same technology stack as Pman. This solution has accrued a large amount of technical debt and is currently supported on aging architecture by CP’s internal DBAs and programmers. The system is unstable, generates spurious results and is hard to maintain.
To solve these challenges, CP was looking for a fresh start to replace their existing systems with a custom system developed using modern architecture and partner with a vendor to assist with supporting their systems.
To evaluate potential vendors, CP requested a proposal and proof of concept (POC) for the replacement of a single module to address Manufacturing Engineering and will select a vendor for the entire project based on the quality of the design and analysis approach taken
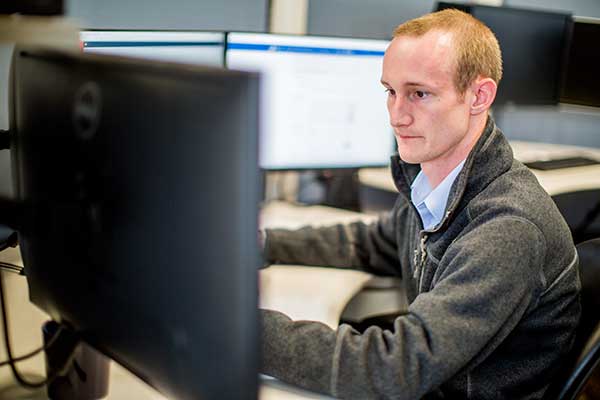
Issue #1
Reduce number of stockouts due to setup/data validation errors, support calls and support time.
Issue #2
Increase the quality of process engineers’ lives and their productivity and increase the talent pool of process engineers.
Issue #3
Reduce learning curve and reduce length of time to set up a new product.
Solution
A more responsive, flexible, and
user-friendly website design.
Orases worked with CP to develop a proof of concept (POC), building out the initial framework and architecture for the new CP systems. The POC included: Single Sign On (SSO; Infrastructure as code; Data in/Data out from existing CP systems; and, Pass CP Internal Security requirements.
As part of the POC, Orases and CP worked together to create an initial roadmap and project plan for the overall modernization of CP’s systems and specifically narrowed down the recommendation(s) for Year 1 (2022) development. Included were: System Diagramming; Finalizing proposed Technical Architecture; Creating a Project Plan for 2022 with estimated costs, timeline and team size; Meetings, Interviews and Collaboration with CP internal stakeholders; and, Meetings, Interviews and Collaboration with 3rd party vendors.
Through the POC process, CP determined they would like to partner with Orases for their long term vision for the CP systems. The next stage was to enter a Pilot together. Orases assigned a discovery, development, quality assurance, and project management team to define, design, and release work requested by CP as it relates to the release 1.0 of the MEM module.
MEM Release 1.0 consisted of a narrow scope that lays the groundwork for the Manufacturing Engineering Module (MEM) which will be used to manage processes at a facility and work center: A basic framework that supports the role of the process engineer; Define, iterate, and refine the module components; Integration between the MEM pilot and legacy applications; and, An ability to assign access and permissions to the module. The initial release is for the US region, and the subsequent release is planned for the UK region.
Project Management Methodology
Technologies Used
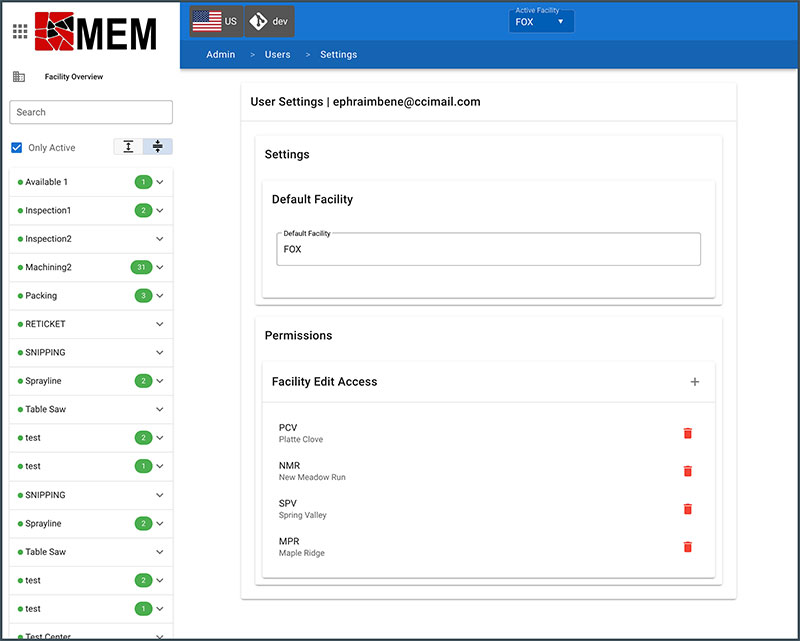
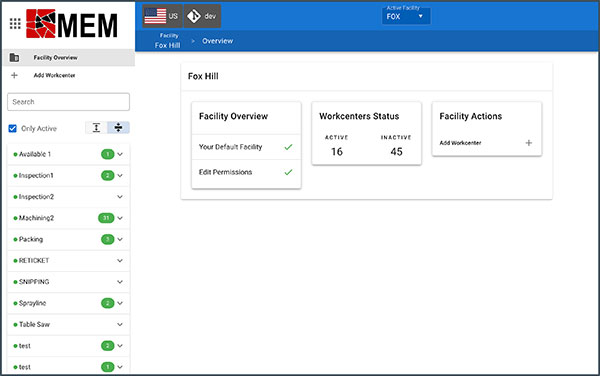
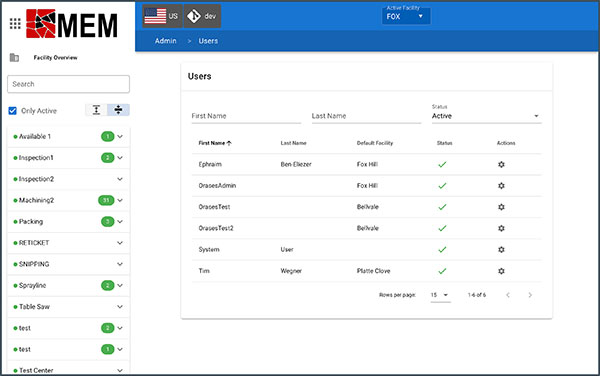
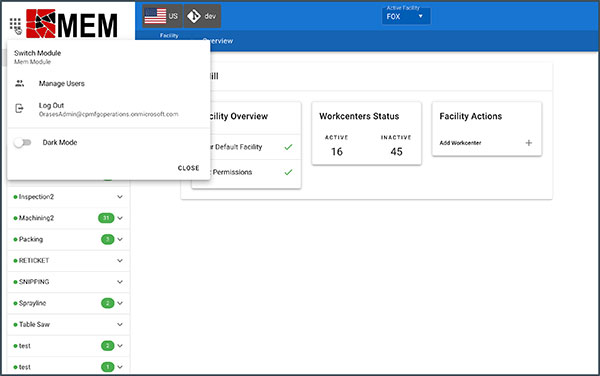
Results
Streamlined system architecture management.
With MEM 1.0, CP has released live to the first subset of users – process engineers in the US region – the first stepping stone of a long term vision for managing their collective CP systems.
MEM 1.0 has also laid the foundation for authentication, permissions, integration and synchronization with legacy data and systems.
Reduction
of stockouts by fixing setup and data validation errors.
300%
Increase in process engineer talent pool.